1.Equipment Introduction
The asphalt pavement maintenance vehicle is a kind of multi-purpose, low-energy-consumption and high-efficiency pavement maintenance equipment. It can conduct thermal insulation transportation of finished materials (mobile), recycling of old asphalt materials, production of new asphalt mixtures, production of new polyurethane road materials, as well as production of colored permeable materials. It is highly suitable for road repair and maintenance, bridge deck paving and repair, production of special materials (such as colored asphalt), and other tasks.
2.Working Principle and Structure
The multi-functional asphalt concrete equipment all features horizontal stirred kettles. In terms of the heating method, it adopts partition heating combined with radiant heating, which boasts high thermal efficiency. The combustion chamber is made of imported 310S high-temperature resistant stainless steel from Germany, and has the advantages of high thermal efficiency and uniform heating. It has a unique unloading method: the screw at the tail discharges materials, and it is hydraulically jacked up. It has the characteristics of fast unloading and the stirred kettle being free from cleaning.
Double horizontal shaft forced stirring
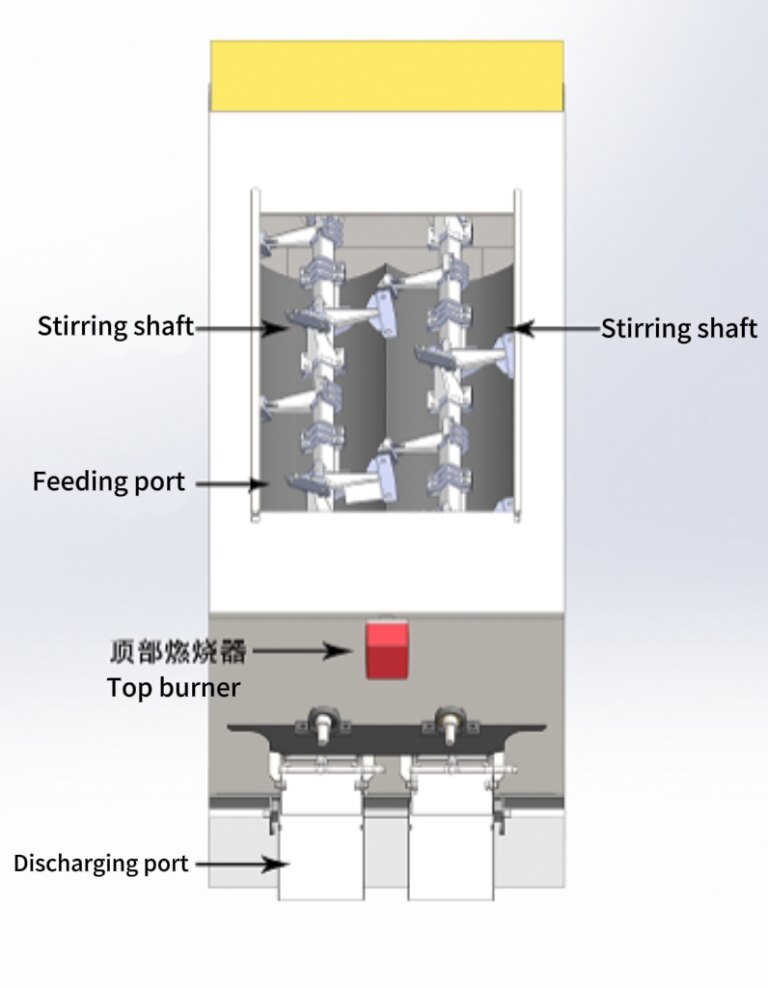
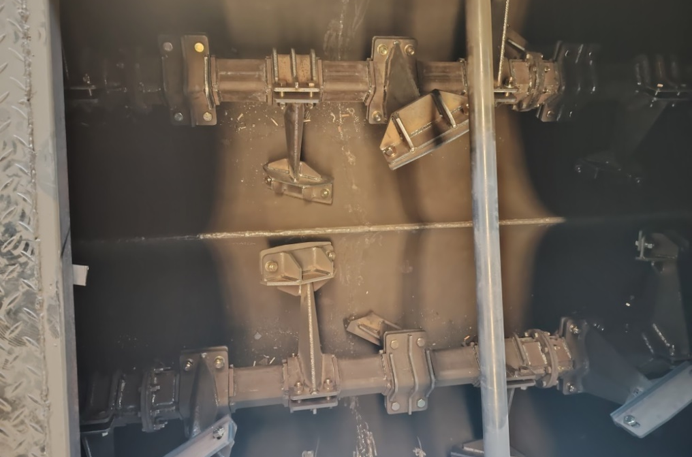
It requires low power consumption. The stirring blades adopt the patented design of the rotary tiller plow type. When stir-frying the old asphalt materials, it can make the materials scatter and form multi-track movements, which is beneficial for the dissipation of moisture and prevents the segregation of materials, thus achieving a more perfect recycled material. It has a powerful power source and runs more stably, ensuring that the asphalt mixture is stirred more evenly.
Unique heating system
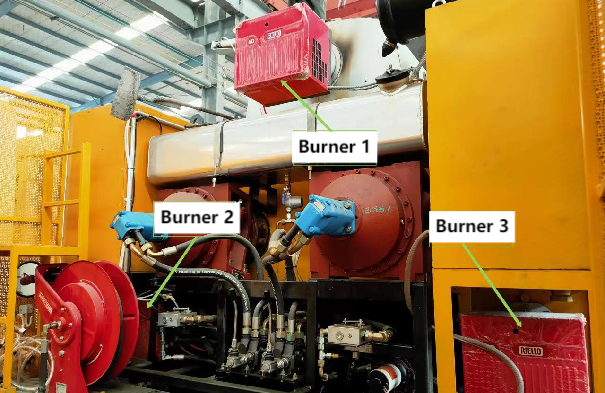
The partition air heating method is adopted, and the combustion chamber is made of imported 310S high-temperature resistant stainless steel from Germany, ensuring that the mixture is heated evenly and there is no temperature segregation.
3.The main components of the special equipment
Include: power unit, stirring kettle, heating system, temperature control system, hydraulic system, thermal insulation system, unloading and discharging system, etc.
① Power unit
The main power is a 55KW motor.
The auxiliary power is a 2.2KW motor.
② Stirring Kettle
Mixing volume: 15m³
Output per single kettle: ≥12,000kg
Stirring method: fully enclosed, rotary tiller type forced stirring
Drive form: hydraulic transmission
Temperature control range: 0 – 240℃,
Heating method: diesel The heating kettle is made of 316 stainless steel, which has a long service life.
Stirring shaft: horizontal stirring, square shaft.
Stirring arm: 12*2
Revolution speed: adjustable, capable of forward and reverse rotation
There is no dead angle, achieving all-round uniform stirring; there is no caked material, unblended material or lumpy material.
③ Heating System Burner model
Riello (Italy)
Power: 238kw per unit, with a quantity of 2 units; 141kw per unit, with a quantity of 1 unit
Total number: 3
It is composed of lightweight aluminum alloy components, a centrifugal fan, an adjustable burner air inlet, a steel air duct, a flame disc, a European-standard automatic control device, and has an electrical protection grade of IP40.
③ Heating System Burner model
Riello (Italy)
Power: 238kw per unit, with a quantity of 2 units; 141kw per unit, with a quantity of 1 unit
Total number: 3
It is composed of lightweight aluminum alloy components, a centrifugal fan, an adjustable burner air inlet, a steel air duct, a flame disc, a European-standard automatic control device, and has an electrical protection grade of IP40.
④ Temperature Control System
Temperature control: The upper limit of temperature measurement is not restricted by the temperature resistance of the temperature-sensing element. The thermistor is small in size and does not cause a thermal load.
⑤ Hydraulic System
It adopts Danfoss 90 series double pumps and piston motors from the United States, and uses PMP7.2 reducers from Italy. The maximum torque of a single shaft is 72,000N.M. The system is equipped with an overload protection system, with a high continuous working pressure of 300Bar, which is stable and reliable. It is equipped with a double radiator.
Rotation direction: Controlled by a handle
Bearing: Ball-and-socket bearing
Power transmission: The hydraulic pump directly drives the hydraulic motor, and the hydraulic motor drives the reducer, which is simple, stable and reliable.
⑥ Thermal Insulation System
Heat dissipation efficiency: ≤3℃/hour
Ceramic silicon fiber + aerogel, resistant to high temperatures and with heat insulation properties
The permanent linear change of HLGX flame-retardant ceramic silicon fiber at 1200℃ for 24 hours is ≤3%.
⑦ Unloading and Discharging
Discharging method: Rotary unloading at the tail. The stirring kettle is equipped with a hydraulic front jacking device, and the jacking angle is ≥30°, with no residual materials