Industry status: According to the 7th edition of the”2025 Construction Industry Aggregate Market Report” recently released by CMR, the global construction aggregate market will reach US$450.85 billion in 2024, with a compound annual growth rate of 5.8% from 2025 to 2034. It is estimated that by 2034, the market will be valued at US$750.98 billion. The traditional fixed production line has an investment return period of 5-8 years. The mobile crushing station can shorten the production cycle to 72 hours with its “ready-to-use + fast transfer” characteristics.
1.Rock properties and the golden rule of equipment selection
Each type of rock and particle size has a specific use case in the construction industry, from fine aggregate in concrete to large stones in heavy infrastructure projects, from residential construction, commercial buildings, infrastructure construction, to industrial projects, so understanding the characteristics of rocks is essential.
1.1 Let’s understand the characteristics of various rocks
Soft rock (Mohs hardness 1-4)
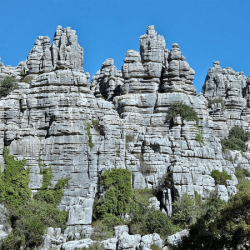
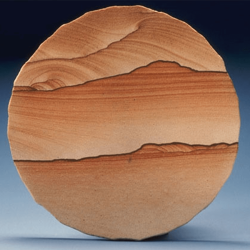
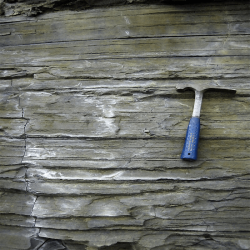
Limestone
Mohs hardness: 3-4
Compressive strength (Mpa): 30-120
Typical applications: cement raw materials, wall blocks
Sandstone
Mohs hardness: 2-4
Compressive strength (Mpa): 20-80
Typical applications: decorative stone, road base
Shale
Mohs hardness: 1-3
Compressive strength (Mpa): 10-50
Typical applications: brick making, lightweight aggregate
Medium hard rock (Mohs hardness 4-6)
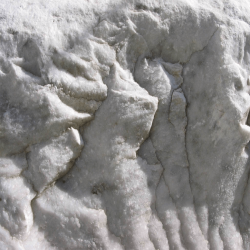
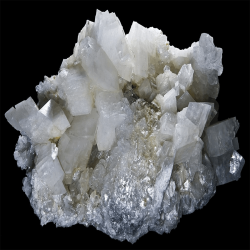
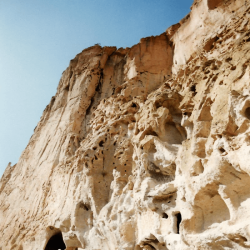
Marble
Mohs hardness: 3-5
Compressive strength (Mpa): 50-150
Typical applications: road paving, sculpture
Dolomite
Mohs hardness: 4-5
Compressive strength (Mpa): 80-160
Typical applications: concrete aggregate, refractory materials
Tuff
Mohs hardness: 4-6
Compressive strength (Mpa): 60-180
Typical applications: building exterior walls, thermal insulation materials
Hard rock (Mohs hardness 6-8)

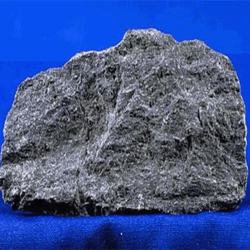
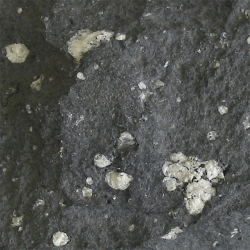
Granite
Mohs hardness: 6-7
Compressive strength (Mpa): 100-300
Typical applications: roadbed aggregate, high-strength concrete
Basalt
Mohs hardness: 7-8
Compressive strength (Mpa): 150-350
Typical applications: high-speed rail sleepers, anti-corrosion engineering
Andesite
Mohs hardness: 6-7
Compressive strength (Mpa): 120-280
Typical applications: water conservancy projects, flood control dikes
1.2 Understand the crushers suitable for rocks of different hardness
Soft rock (level 1-4): shale, marl → suitable for hammer crusher and impact crusher (crushing ratio 15:1)
Medium hard rock (level 4-6): limestone, sandstone → standard jaw crusher + impact crusher + pre-screening system
Hard rock (level 6-10): granite, basalt → must use cone crusher with laminated crushing principle
1.3 The impact of abrasiveness index (AI value) on equipment wear
Rock Type | AI Value Range | Wear Parts Replacement Cycle |
Limestone | <0.3 | 600-800 hours |
Granite | 0.5-0.7 | 300-500 hours |
Quartzite | >1.0 | 150-300 hours |
2. Precise control of aggregate gradation
2.1 Requirements of construction standards for aggregate particle size
Note: The local requirements and standards in different regions are inconsistent. The data in the table is based on the average market situation of the construction industry and is for reference only.
Type | Particle Size(mm) | Uses |
Quarry Dust (Fine Aggregate) | 0-5 | •Used in concrete production as a sand substitute •Filling voids and leveling surfaces in road construction |
Sand(fine to Medium Aggregate) | 0-6 | • Core ingredient in concrete and mortar production. • Utilized in plastering and pavement works. |
Small Chippings (Coarse Aggregate) | 6-10 | • Used in decorative concrete surfaces. • Applied in block manufacturing. |
Medium Chippings (Coarse Aggregate) | 10-20 | Commonly used in general concrete work and road construction. |
Large Chippings (Coarse Aggregate) | 20-40 | • Used in heavy-duty concrete applications such as bridges and foundations. |
Crushed Rock (Ballast/Hardcore) | 40-150 | • Applied in railway ballast for track stability. • Used in road base layers and drainage works. • Utilized in embankments and heavy-duty foundations |
Boulders (Rock Fill) | >150 | • Used in breakwaters, ero–sion control, and retaining walls. • Applied in dam construction and large-scale infrastructure projects |
2.2 Clarify the equipment for precise matching of aggregate particle size
Taking the standard of concrete aggregate diameter for house construction as an example, according to industry standards and specifications, concrete aggregates are divided into fine aggregate (sand) and coarse aggregate (gravel), and the specific specifications are as follows:
Bone material
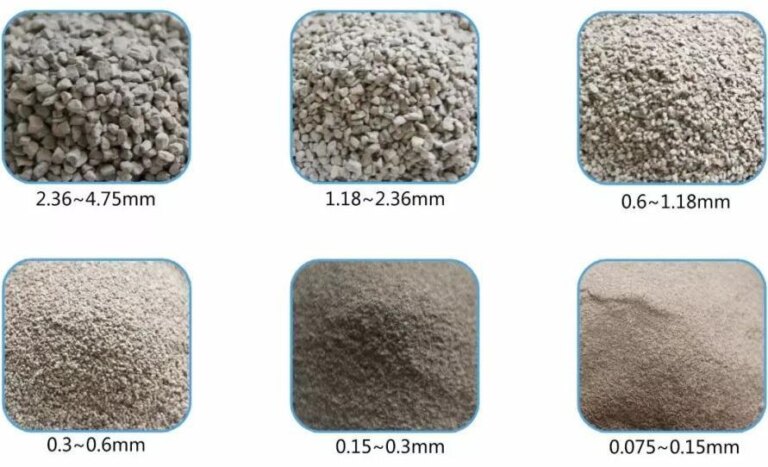
Particle size range: 0.15~4.75mm
Classification:
Coarse sand: fineness modulus 3.7~3.1, average particle size ≥0.5mm;
Medium sand: fineness modulus 3.0~2.3, average particle size 0.5~0.35mm (recommended for ordinary concrete);
Fine sand: fineness modulus 2.2~1.6, average particle size 0.35~0.25mm
Coarse bone material
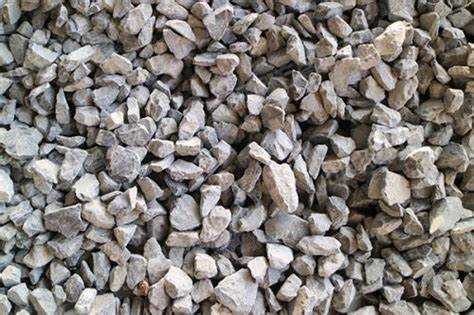
Particle size range: 5~40mm (common specifications are 10~20mm, 16~31.5mm, etc.)
Typical classification
1-2 gravel: 10~20mm (for concrete surface and roads);
1-3 gravel: 16~31.5mm (suitable for high-strength concrete);
5-10mm melon stone (for special filling)
2.3 Production process from rock feed to crushed finished product
Primary crushing (coarse crushing)
Equipment: jaw crusher (feed ≤ 1200mm, discharge 150~300mm);
Function: crush the raw materials to a size suitable for secondary crushing.
Secondary crushing (medium crushing)
Equipment: cone crusher or impact crusher (discharging material 40~70mm);
Technical points: Pre-screening to remove over-limit stones and improve grade matching rate.
Three-stage crushing (sand making)
Equipment: vertical shaft impact crusher (discharging 0~5mm machine-made sand, fineness modulus 2.6~3.0);
Case: A commercial concrete mixing station in Côte d’Ivoire, Africa, achieved a grade matching rate of 95% through “jaw crusher + cone crusher + sand making machine”.
3. Output calculation and equipment selection
3.1 Hourly output calculation formula and key parameters
Basic calculation formula
Q(hourly production)= total aggregate demand/(construction period (days))*daily working hours*K)
K: production capacity correction factor (value ranges from 0.7-0.9, including equipment maintenance, weather effects, etc.)
3.2 Comparison of project scale and equipment configuration
Small projects (output ≤ 50t/h)
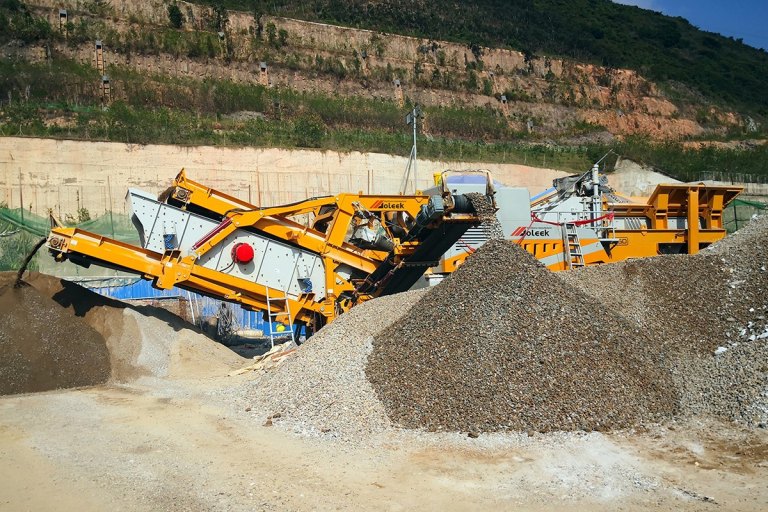
Recommended configuration:
Main unit: tire-type jaw crusher
Auxiliary equipment:
Vibrating feeder (processing capacity ≤ 100t/h)
Single-layer vibrating screen (screening accuracy ±3mm)
Advantages:
Transfer time ≤ 2 hours
Investment cost ≤ $ 85
Medium-sized projects (50-200t/h)
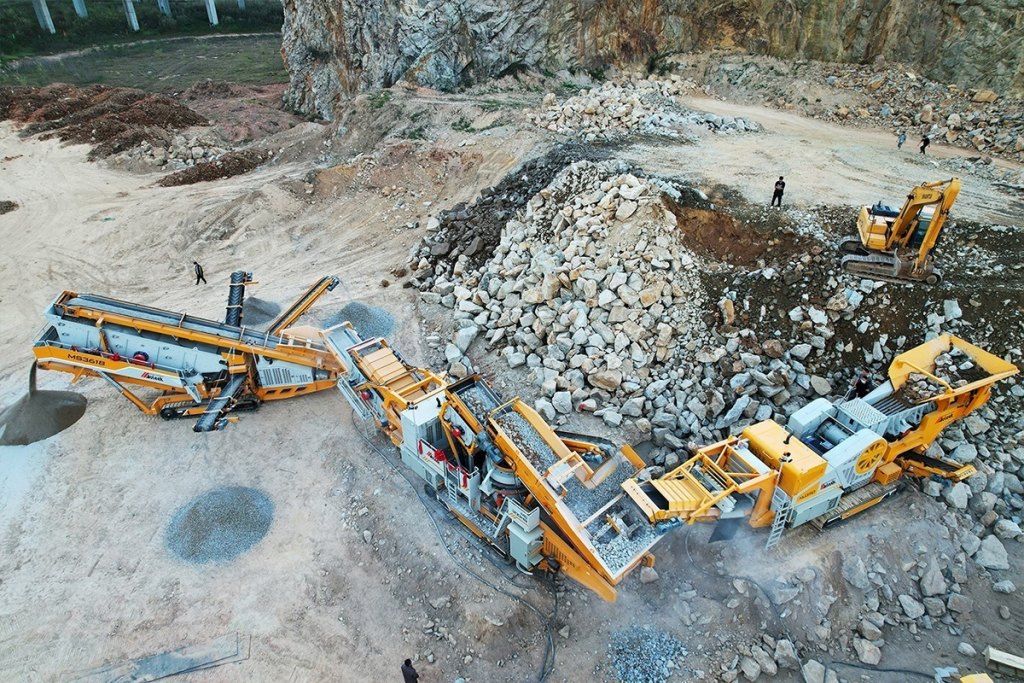
Main unit combination: crawler jaw crusher + cone crusher
Auxiliary system:
Three-stage screening (4.75/16/31.5mm classification)
Pulse dust removal system (emission ≤30mg/m³)
Advantages:
Grade matching rate ≥90%
Energy consumption ≤2.5kW·h/ton
Large projects (output ≥ 200t/h)
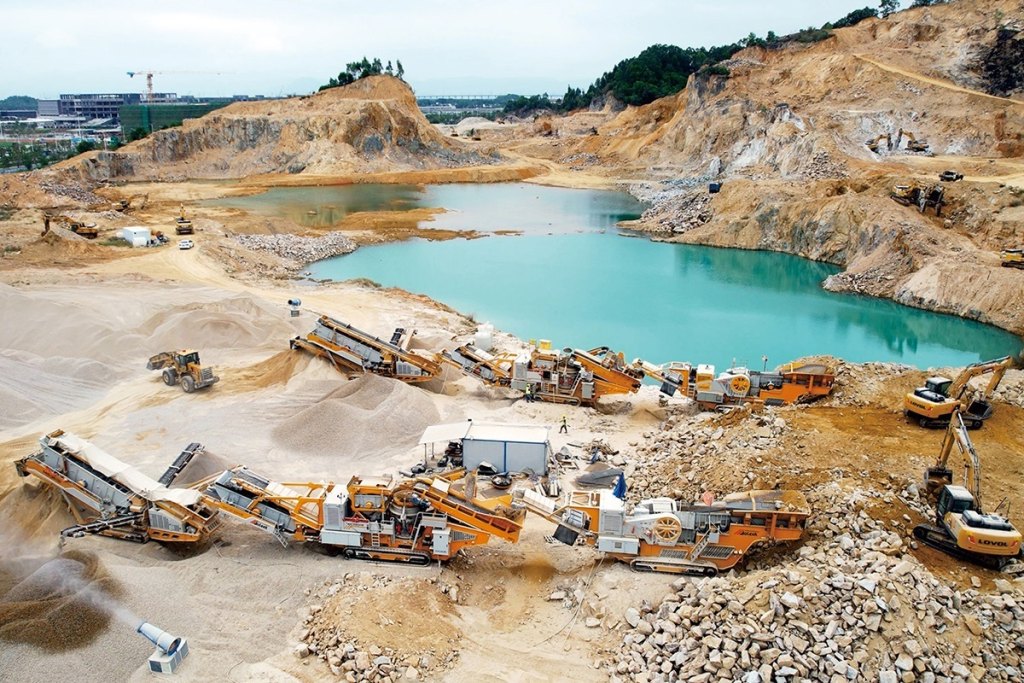
Recommended configuration:
Host combination: modular jaw crusher + multi-cylinder cone crusher + vertical shaft sand making machine
Intelligent system:
PLC central control system (remote fault diagnosis)
Automatic lubrication system (oil injection error ≤±3%)
Advantages:
Support 24-hour continuous operation
Finished sand fineness modulus is adjustable
4. Intelligent operation and maintenance system selection guide
4.1 Intelligent module selection
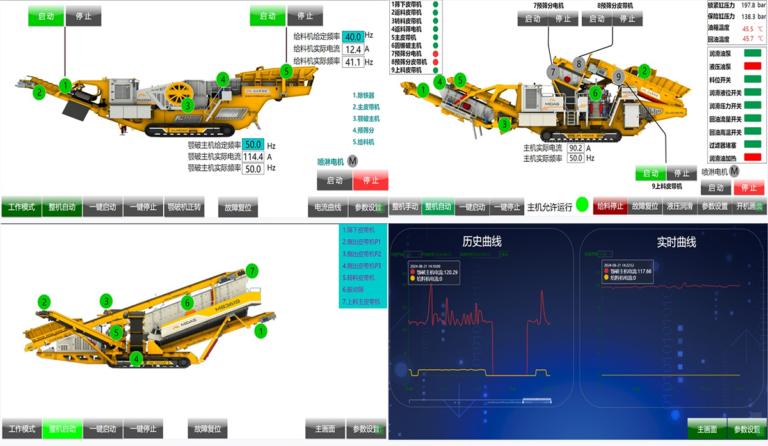
PCL control system: The operator can start and stop the machine with one button on the touch screen, which reduces the errors easily caused by traditional button control. The operation interface can display the working status of each module and system parameters in real time. For example: the actual working current of the crushing main motor, the real-time frequency, the start-up interval of each module, the working pressure of the hydraulic/lubrication system, etc.
Production statistics module: Automatically generate daily reports (support EXCEL/PDF export), count the project progress by week or month, and plan the follow-up work.
4.2 Environmental protection configuration selection
Pulse bag dust collector: The processing air volume needs to match the production capacity (for example, a 1000t/h production line needs a processing volume of 200,000 m³/h), and the emission concentration is ≤30mg/m³ (GB 4915-2020 standard).
Spray dust suppression device: A high-pressure water curtain is set at the feed inlet and the conveyor transfer point, and the dust suppression efficiency is ≥85%.
Sealing design: Fully enclosed belt conveyor and crusher negative pressure cover to prevent dust from overflowing
Shock-absorbing foundation: Use rubber isolation pads or spring shock absorbers to reduce equipment vibration transmission.
Low-noise equipment selection: Hydraulic cone crusher is preferred (the noise is 5~10dB lower than jaw crusher)
Summarize
Scientific selection requires comprehensive consideration of rock characteristics, grading requirements, production capacity, intelligence and environmental protection needs. For example, a hard rock project requires a cone crusher + intelligent system. It is recommended to adjust the configuration through professional research and investigation processes in combination with local standards to ensure maximum return on investment.