The conveyor belt produced by a listed company is adopted, ensuring reliable quality. An EP polyurethane conveyor belt with a greater tensile strength in a single layer is selected. The tensile strength of a single layer reaches 300N/mm², and the belt has 5 layers. Its comprehensive tensile strength is several times that of an ordinary belt. Compared with an ordinary N conveyor belt, it has a lower elongation rate and will undergo less deformation even after long-term use.
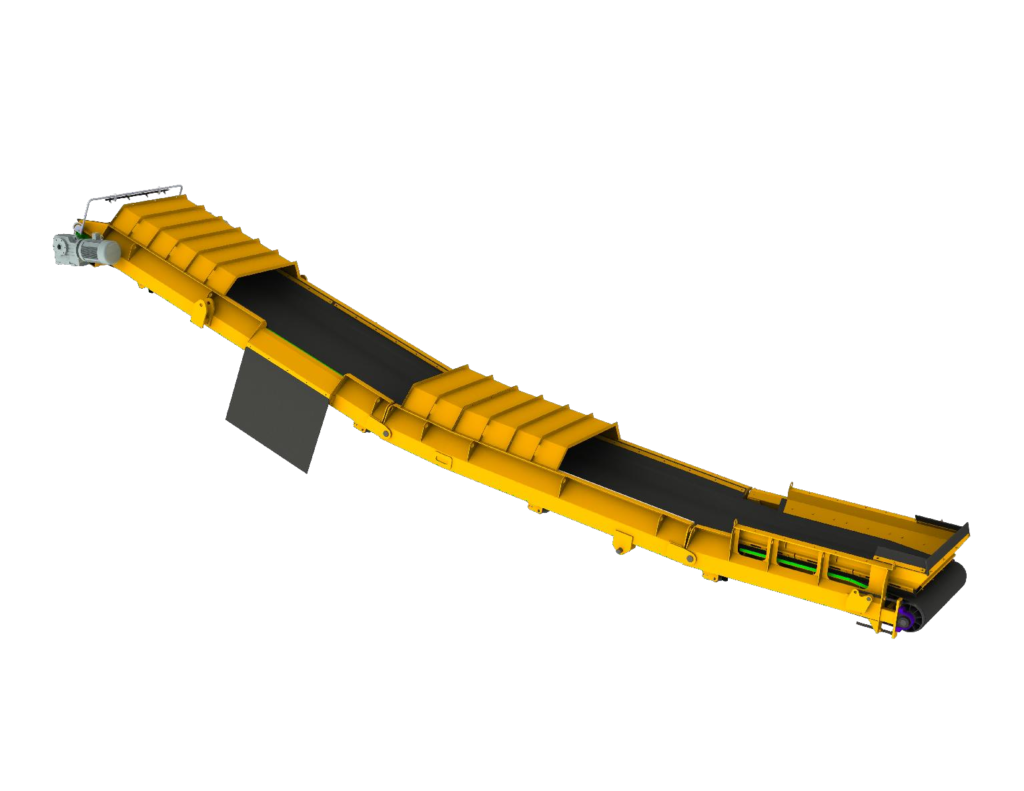
An independent pre-screening machine is adopted, which can conduct a thorough pre-screening of the raw materials. The materials in the raw materials that are smaller than the finished products will be pre-screened by the grate bars and then enter the main belt conveyor (finished products) or the side-out belt conveyor (fine dust materials). This effectively reduces the working load of the main crushing machine, which is equivalent to increasing the output in a disguised form. At the same time, it can provide sufficient crushing space for the main machine to crush large pieces of materials, reduce the wear and tear of the wearing parts caused by the fine materials, improve the efficiency, and lower the production cost.
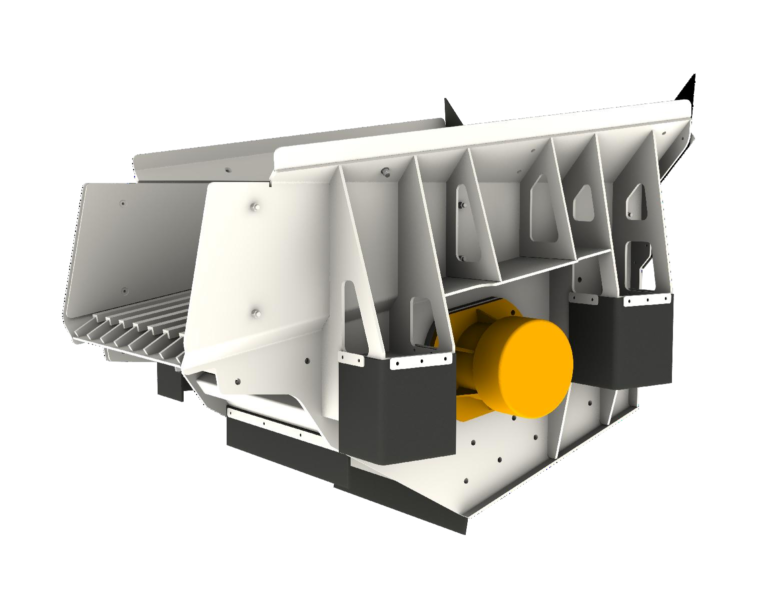
The pre-screening machine and the feeder are equipped with separate frequency converters. When the material level in the crushing chamber reaches the warning height, the sensor sends a signal to reduce the voltage frequency of the feeder and the pre-screening machine, thereby reducing the feeding volume. When the material level in the crushing chamber drops below the warning height, the sensor sends a signal to restore the voltage frequency of the feeder and the pre-screening machine to normal, resuming normal feeding. This effectively avoids the trouble of overloading and blockage, which would otherwise require material cleaning.
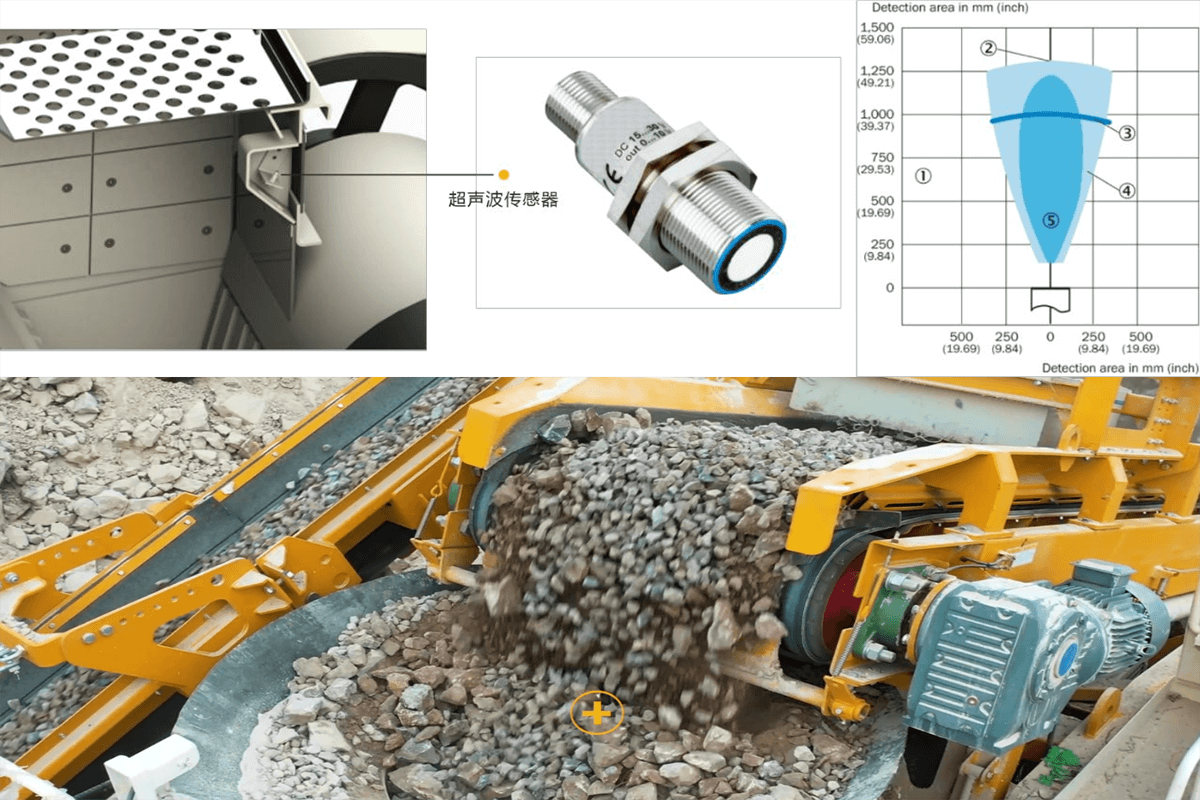
The new generation of reinforced steel frame adopts a full range of heavy-duty structural designs. The Q355B material with higher strength and better low-temperature performance is selected. The overall vehicle frame undergoes CAE analysis and verification through 3D software. The areas with the greatest working stress and the weak links of the structural components are strengthened as a whole to improve the impact resistance of the vehicle frame, making the whole machine more stable during operation and having a longer service life. The impact resistance and service life of the overall vehicle frame exceed those of similar products in the industry by more than 20%.
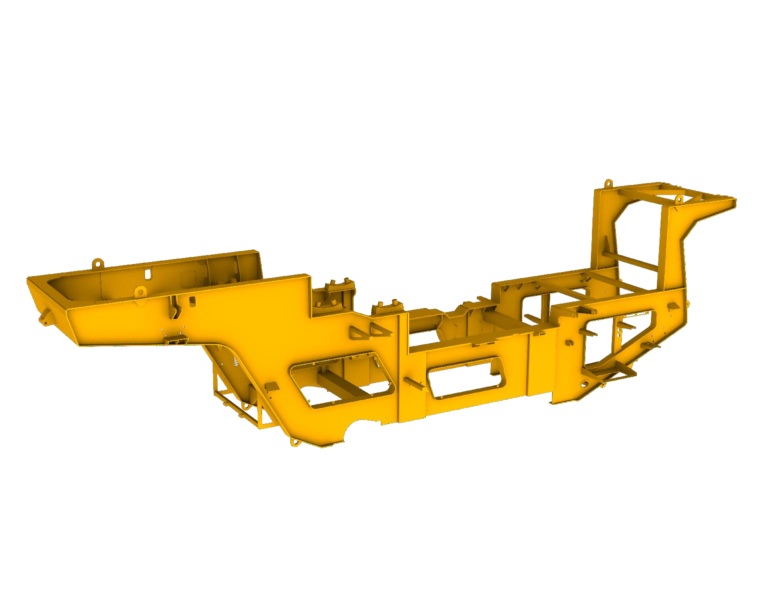
It adopts Siemens brand PLC controllers and touch screens, which feature stable performance. The operation page can display the working status of each module, system parameters, etc. in real time, enabling you to keep track of the status and progress at all times. In addition, it also has functions such as remote background detection and control, and one-click operation.
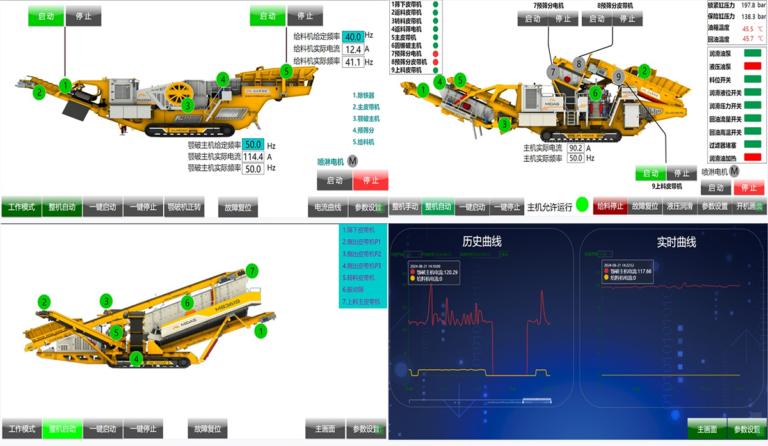
The integrated vibrating feeder, jaw crusher, multi-cylinder hydraulic cone crusher, three-layer double-section screen, and four units not only significantly reduce the occupied space, but also improve the crushing efficiency. Through the ingenious structural design, it achieves the crushing and screening effect equivalent to that of a separate hard rock production line.
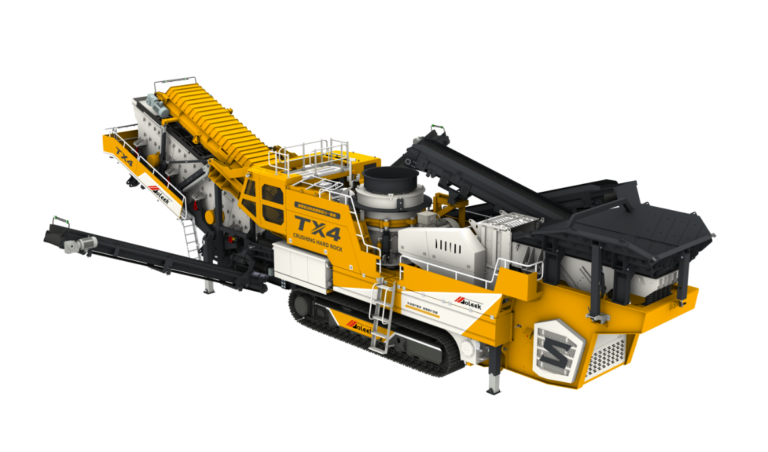